Testen von Leistungselektronik
Herausforderungen beim Testen von Leistungselektronik
Reale Bedingungen darzustellen, das ist offenbar Hürde herkömmlicher Testverfahren. Deshalb ist unser Prinzip ein anderes.
Herausforderungen
Wo herkömmliche Testverfahren ein gravierendes Manko haben
Bei Qualifikationsprüfungen von Leistungselektronik stellt sich meist die Frage nach dem, was in einem Testaufbau „real“ vorhanden sein muss – und worauf verzichtet werden kann.
Besonders gut lässt sich diese Frage beispielsweise an einem Antriebsinverter – einer sehr komplexen Leistungselektronik – illustrieren, kann aber auf jegliche Leistungselektronik sinngemäß übertragen werden:
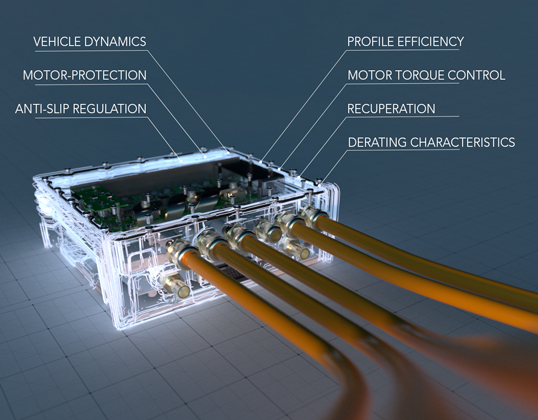
Zunächst ist zu klären, welche Spezifikationspunkte in welcher Testanordnung verifiziert werden sollen. Dies betrifft einerseits den Prüfling selbst und andererseits die hierzu erforderliche Testumgebung. Aufgrund der hohen Leistung, Spannung und Ströme, die typischerweise von einem Antriebs-Inverter geregelt werden, besteht eine Tendenz, auf die Leistungskomponenten des Gerätes für den Testprozess komplett zu verzichten. Hintergrund ist: Handelsübliche Hardware-in-the-loop Systeme (HiL) sind nur im Kleinsignal-Bereich erhältlich (Signal-HiL). Folge: Der Testaufbau wird dadurch stark vereinfacht – allerdings verlieren die Tests bei einer solchen Vorgehensweise auch massiv an Aussagekraft.
Denn für die Testdurchführung wird in diesem Fall der originale Prüfling stark manipuliert („Cracked-ECU“-Verfahren) und alle Teile des Prüflings, die in irgendeiner Form mit elektrischer Leistung, hohen Strömen oder hoher Spannung in Verbindung kommen, werden ausgebaut bzw. deaktiviert. Die dadurch verloren gegangenen Funktionen des Prüflings werden dann hilfsweise durch Modelle (in Hardware und Software) ersetzt, um eine geschlossene Funktion dennoch „vorgaukeln“ zu können.
Von einem Leistungsinverter bleibt für den Testprozess bei diesem Verfahren also kaum mehr Hardware übrig und das Testobjekt hat nicht mehr viel mit dem ursprünglichen Prüfling gemeinsam – meist nur noch die (manipulierte) Rechnerkarte.
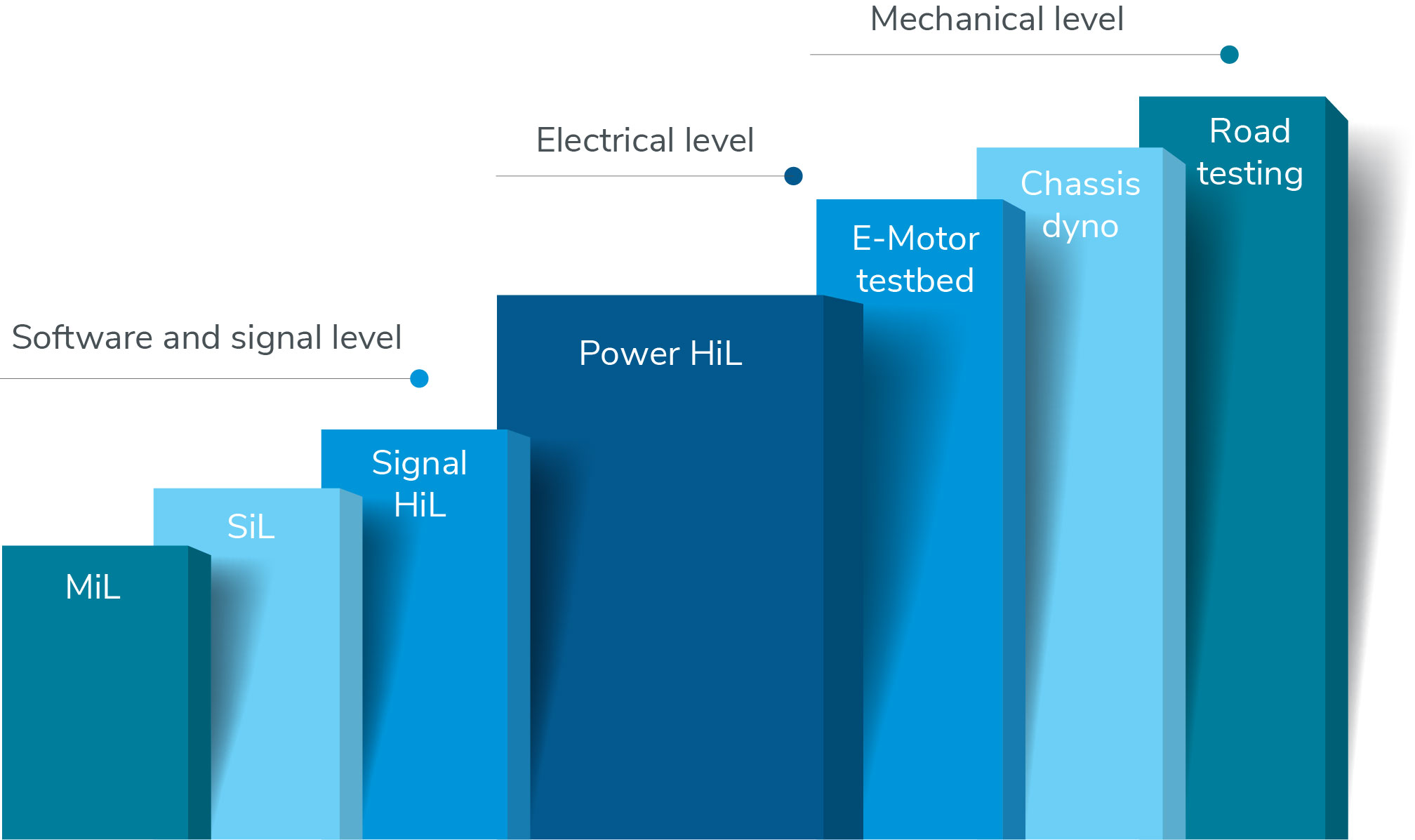
Sicherheitsrelevante Tests – und damit qualifizierte Aussagen – sind in diesem Verfahren nicht möglich, da der Prüfling seinen originalen Charakter verloren hat. So lassen sich mit diesem Testverfahren lediglich grundsätzliche Fragen hinsichtlich Reglerarchitekturen, Software-Funktionen oder einfach zum Signalrouting der Prozessorkarte ausreichend gut beantworten. Weitergehende Validierungsprüfungen an der gesamten Leistungselektronik sind mit einem solchen Prüfaufbau jedoch nicht möglich.
Zwischen diesen beiden Testansätzen besteht also eine eklatante „Lücke“. Von einem Signal-HiL Aufbau zum Test des Inverters mit der realen Maschine ist es ein großer Schritt mit vielen Unwägbarkeiten. Zu Ihrer Beruhigung: Wir haben die Test-Lücke überwunden.
Statt Manipulation:
Wie Sie mit AVL SET die Test-Lücke schließen können?
Um die gesamte Leistungselektronik – in unserem Beispiel einen Antriebsinverter – entwicklungsbegleitend mit einem Validierungsanspruch (hinsichtlich Hardware und Software) zu testen, ist es erforderlich, eine geeignete Testumgebung zu realisieren, die ausreichend genau reale Verhältnisse an den Schnittstellen des Inverters herstellt. Seitens der DC-Versorgung kann dies durch die reale Hochvolt-Batterie und seitens der Phasenanschlüsse durch die reale E-Maschine erfolgen, wobei die E-Maschine zwecks Belastungsszenarien an ein Dynamometer angeflanscht werden muss. Grundsätzlich kommt auch ein Aufbau in Betracht, bei dem der Dyno durch eine zweite E-Maschine (Belastungsmaschine) ersetzt wird.
Grundsätzlich unterscheiden wir beim Testen zwischen Validierungsprüfungen und Produktionstests (End-of-line-Test, EoL). Lebensdauerprüfungen sind eine Teilmenge der Validierungsprüfungen. Die Prüfung von Feldrückläufern nach einer erfolgten Reparatur ist – je nach Ausprägung des Produktes und dem Produktionsverfahren ggf. eine weitere Prüfanforderung. Hierbei handelt es sich nicht um einen erneuten Qualifizierungstest (Typprüfung). Oftmals besteht hier die Lösung in der Nutzung des Testsystems, welches für die Produktqualifikation eingesetzt wurde.
Mit welchen Herausforderungen beim Einsatz realer Komponenten zu rechnen ist?
Und unsere Lösung …
Batterie
Eine mechanische Anordnung, wenn also reale Komponenten, die Batterie und der E-Motor, zum Einsatz kommen, birgt insbesondere durch die Batterie ein erhebliches Gefahrenpotenzial, bringt Alterungseffekte, thermische Aufgabenstellungen, Ladezustände und vieles mehr an unerwünschten Nebeneffekten mit sich. Unsere Konsequenz?
Wir ersetzen die reale Batterie für den Test der Leistungselektronik durch eine emulierte Batterie, einen sog. Batterie-Emulator. Bei Systemen, die eine Brennstoffzelle als Energiequelle nutzen, wird dementsprechend die Brennstoffzelle durch eine geeignete Gleichstromquelle ersetzt. Sinngemäß ergibt sich dieselbe Problematik auf der AC-Seite des Antriebsinverters.
Eine reale E-Maschine muss geeignet belastet werden, hat Exemplar-Streuungen, thermische Effekte, Verschleiß und damit viele Nebeneffekte, die bei der Prüfung der Leistungselektronik unerwünscht sind. Zudem ist die E-Maschine oftmals nicht rechtzeitig verfügbar, weil sie sich noch in der Entwicklung befindet oder nur einzelne Prototypen vorhanden sind.
E-Maschine
Das zentrale Problem beim Testen mit einer realen E-Maschine ist jedoch, dass eine Integration von Inverter und E-Maschine zu einem Zeitpunkt erfolgen muss, an dem nur die Leistungselektronik getestet werden soll – unabhängig von der E-Maschine. Dabei werden zwei Komplexitätsebenen vermischt: die elektrische Ebene des Inverters mit der mechanischen Ebene der E-Maschine.
Prüfungen von Invertern werden dadurch langwierig, unnötig komplex und erlauben trotzdem nur eine mangelhafte Testtiefe. So kann in solch einem mechanischen Aufbau die Prüfung von Fehlerreaktionen nur unzureichend erfolgen. Hinzu kommt, dass ein Dynamometer immer nur eine begrenzte Regeldynamik aufweist und beispielsweise Lastmomente bei sehr kleinen Drehzahlen oszillieren.
Seitens des Prüflings – dem Inverter – muss bereits eine funktionierende Maschinenregelung implementiert sein, um die ersten Versuche erfolgreich durchführen zu können, ohne den Prüfling bzw. die E-Maschine zu beschädigen.
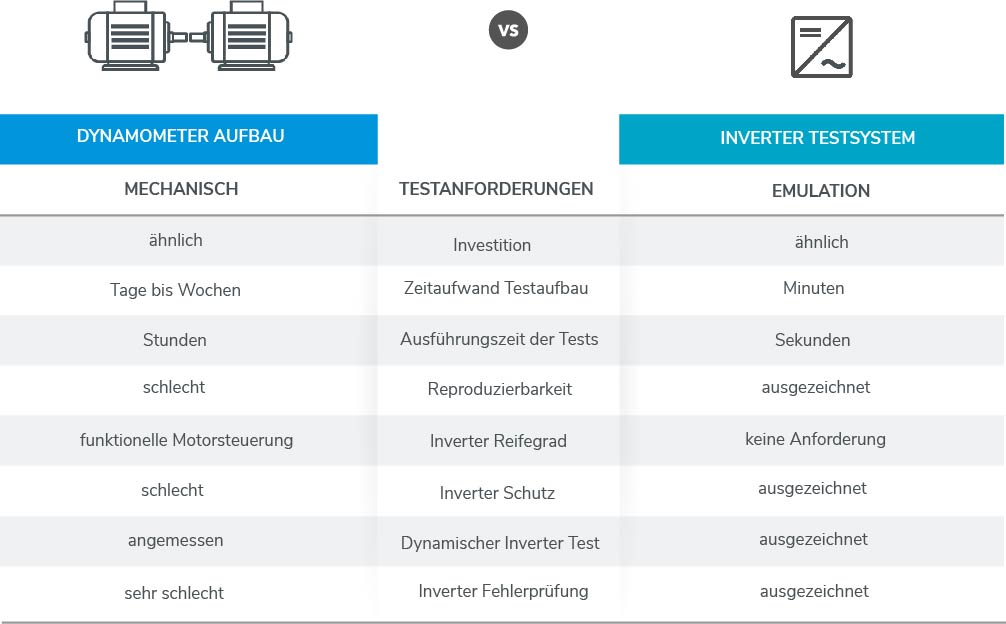