Application
Production of power electronics
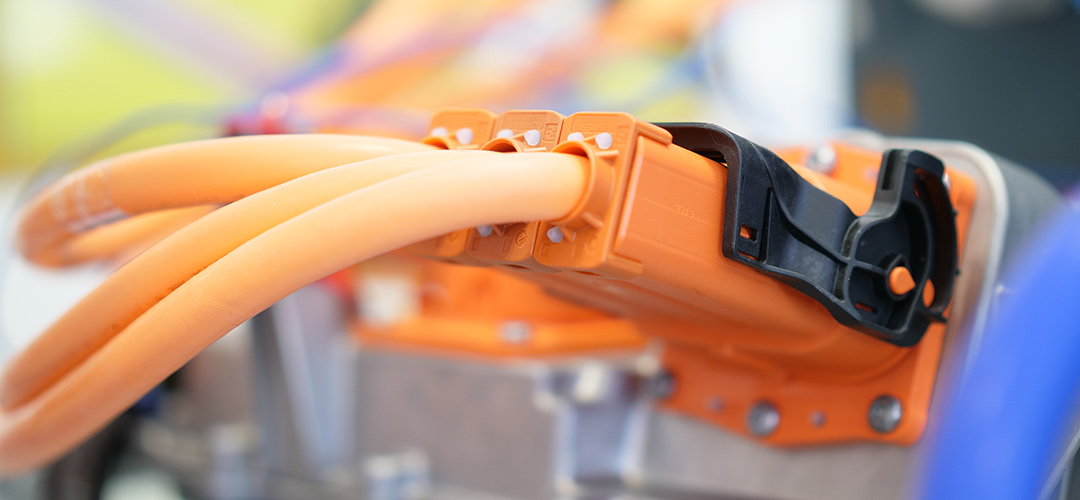
There are three topics concerning the production of power electronics that are of huge significance:
- Production costs
- required production time per device
- and conformity with the required production quality.
Production
Saving in the right place? Not at the expense of quality.
Specialized production lines have been established for the production of power electronics in which the devices are automatically assembled from individual components. Automated tests are conducted in parallel to device assembly, right up to the so-called end-of-line tests, which check the correct functioning of every manufactured device.
An important criterion for these device tests is the time required to carry out the test on the production line. The required number of production lines results from the specified production volume per year and the production and test time per device. Test times on a production line are typically in the range of 1 to 2 minutes per device.
PRODUCTION
Two test procedures can be considered for drive inverter testing on a production line
They differ in the type of motoring load. AVL SET offers solutions for both load types as well as dielectric tests and calibration:
Passive Load
Active Load
Testing with a passive load requires connecting an inductive-resistive load to the phase connections of the unit-under-test. The rotor sensor is emulated to enable the simulation of a rotating motor.
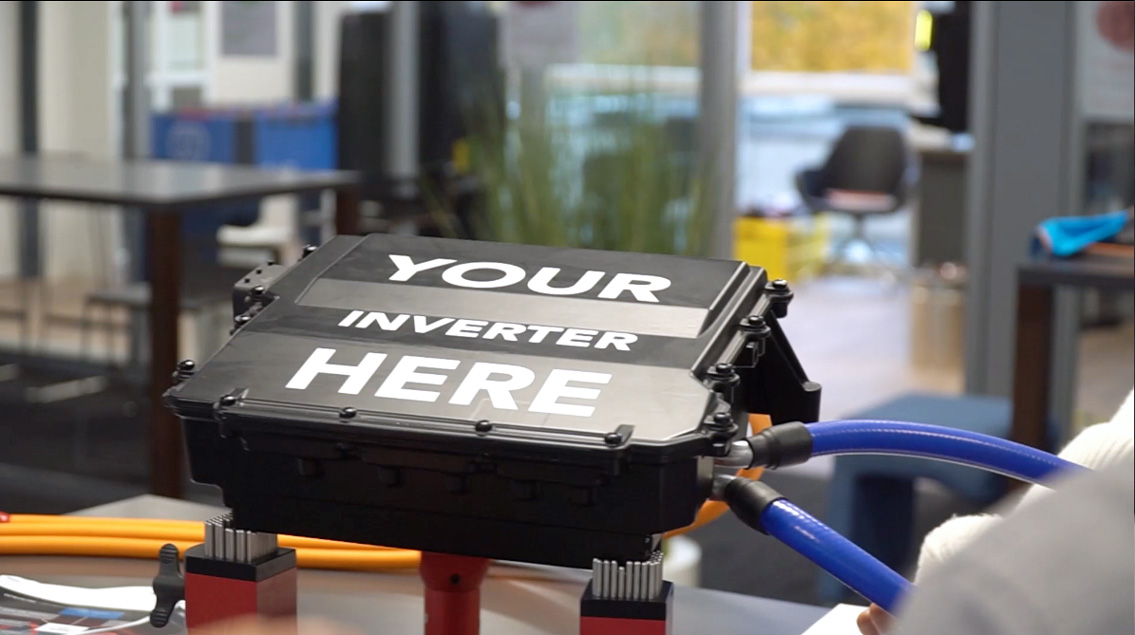
Testing
Active Load
These compromises can be eliminated by using an active load and the load on the phases is achieved through a combination of inductance and multi-quadrant amplification.
Recuperation is possible with this test layout and energy flows in a circuit rather than is converted into waste heat. The disadvantage of this solution are the higher costs due to the required bi-directional amplifier.
Testing
Passive Load
The costs for a passive load are moderate. The disadvantage of a passive load are the power losses in the resistive load share that can be very high and therefore usually must be conducted away with liquid cooling. Apart from the heat losses, this solution also entails energy costs that along with the cost factor are no longer in the spirit of the times of energy conservation. A further disadvantage is the load simulation that is based on a rigid inductance and therefore only very approximately mirrors real e-motor conditions.
This disadvantage is generally acceptable for end-of-line tests. However, such a test layout does not offer any recuperative behaviour and tests in these quadrants are not possible. If the resistive component in the load is selected too low, although the energy consumption falls, hardly any energy flows in the DC side of the unit-under-test. Quality issues may not be recognized.