Power Electronics Testing
Testing Methodology
Only with a test process in place will the product be as good as it has to be.
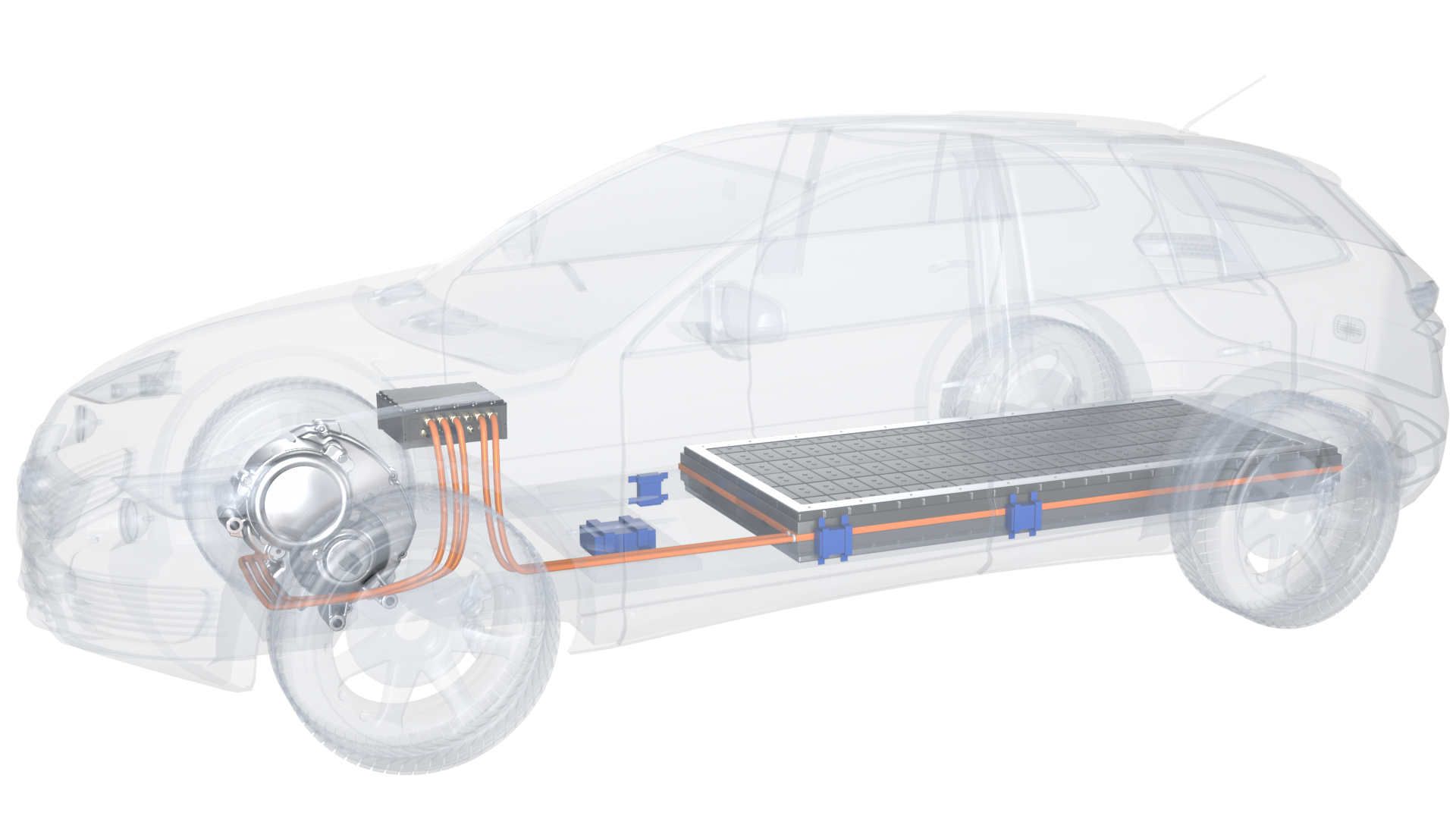





Testing Methodology
Why should you test power electronics?
Only with a test process in place will the product be as good as it has to be. What is the logic behind this?
Everything that has been “specified” for a future product, or defined, has to be “validated”. This means that the defined features have to be proved in the development process, otherwise defining product features would be a waste of time. This is also true for the product “power electronics”.
Why do we focus our attention on the testing of power electronics?
Generally speaking, power electronics consist of all components involved in the conversion of electrical energy. This has associated energy losses. The resulting component heating means that this conversion is done predominantly by electronic switching elements.
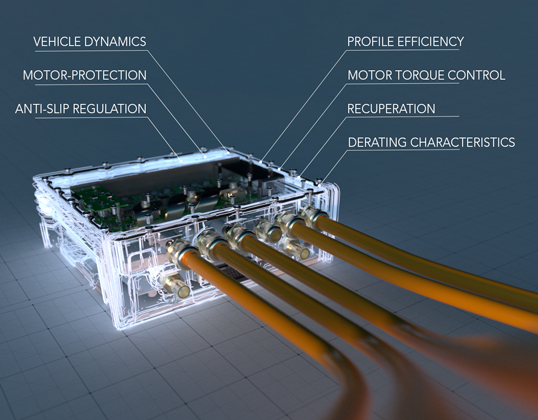
Power Electronics
Heart and brain of electric powertrains
Power electronics in the form of an inverter is one of the three core elements in every electrical powertrain (hybrid or EV): Energy storage / inverter / e-motor. The inverter plays a major role (alongside other power electronic devices such as charge controller, voltage converter or auxiliaries such as steering servo or electric brakes). From an electrical engineering perspective, the inverter converts the energy stored in the battery, i.e. direct current, into a suitable three-phase alternating current for the e-motor. To do this, the inverter detects the position of the e-motor’s rotor and provides the phases of the e-motor such that the desired torque appears on the e-motor’s drive shaft.
E-Motor
So there is no “intelligence” in the e-motor itself.
The same is true for energy storage (battery or fuel cell): Apart from the required safe operation, there is no form of intelligence present in the form of software.
This means that power electronics play a particular role in the group of the three core electrical elements: It converts the direct current into alternating current for the drive. And it controls the e-motor torque in real-time. To do this, apart from the components required to handle the power, the power electronics module also contains a mini-computer and comprehensive software to handle functions such as anti-skip, anti-slip and recuperation. The power electronics module communicates with superordinate devices, carries out diagnostics, and monitors e-motor loading.
Power electronics are
the “heart and brain” of an electrical powertrain.Â
The higher the number of requirements defined, or specified, for a product, the more comprehensive the validation process becomes: The “testing”. In the case of power electronics, the requirements are not only comprehensive but also complex. On the one hand, ambitious electrical KPIs need to be proven, and on the other, complex software algorithms and safety functions need to be checked.
Software testing is a particularly interesting aspect. Software “grows” and is “debugged”. This process accompanies the power electronics product over its entire life-cycle and is usually required for several product variants.
Where are you wasting time?
Which faults should not occur?
It is important that the tests are carried out in a manner that comes as close to real situations as possible. Tests performed on power electronics where all power elements are switched off do not conform with this requirement. Tests that deliver results under laboratory conditions that are different to those results obtained in real use-cases are, best case, a waste of time.
A good test strategy needs to be in place at the latest when the power electronics are integrated with the e-motor. If faults are only discovered in the power electronics during integration with the e-motor, then you are clearly being confronted with weaknesses in the test strategy.
What are the consequences of an inadequate test strategy?
The effort of correcting faults during the integration process is considerably higher. And the consequences could be additional project costs, project delays, recall actions and safety risks. It is therefore important, that faults are eliminated in the development phase of power electronics.
Our motivation? To make available an efficient test methodology for power electronics that is as close as possible to reality.
Once the power electronics module has been successfully validated via meaningful, close-to-reality tests, also with regard to the expected lifetime and environmental aspects, the module progresses to series production. The topic of testing is again on the agenda to ensure that any deviations in quality such as devices with production faults or component faults are recognized. The test requirements change. That is why we provide adapted solutions that enable power electronics to be tested within a few seconds in an end-of-line application.