Application
Development of Power Electronics
Frictionless cooperation between many different expert disciplines such as electronics development, software development, cabinet design, thermal management, EMC, and control technology to name just a few is required to develop a product suitable for market launch.
 Other key topics include the selection of components, maintaining conformity with all standards and taking manufacturability and testability on the production line into account.
We see the following recurring goal conflicts that compromise the development of components for power electronics:
Small and yet powerful
Long lifetime and yet low-cost
High degree of efficiency and yet for all operating points
Do you experience this balancing act every day?
So do we. That is why we worked on solutions.
Development
What is a suitable solution for the investigation of power electronic performance in parallel to development work?
The development of power electronics is closely linked to a lot of simulation activity to ensure that all requirements are covered. This is the only way to find the architectural optimum for the components and hence combat target conflicts. We put you into the position of being able to conduct tolerance observations in order to guarantee the specified characteristics in later production batches. We support you during the development phase by providing a suitable testing environment that enables you to directly verify solutions and sub-solutions.
Your power electronics can only be as good as the test procedure
Allow us to demonstrate the requirements using a drive inverter project as an example:
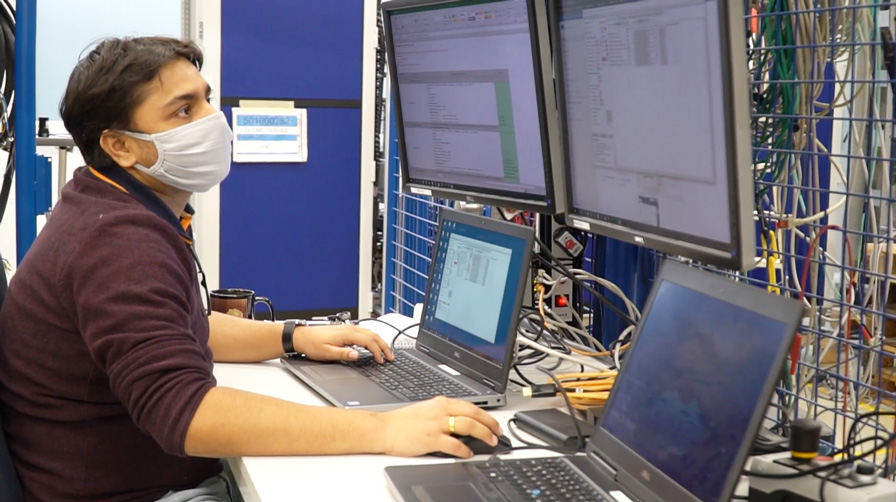
Representation of the basic maximum electrical data required by the project
This data includes the maximum phase current, maximum and minimum intermediate circuit voltage, maximum power, and design of the required phase number. The test solution should also cover future requirements for subsequent projects: covering future demands, separately excited e-motor, more than three phases, or an extension of the basic electrical data. Modularity and subsequent extendibility are important criteria for the selection of a test solution.
Representation of test scenarios for one still incomplete unit-under-test
We want to enable you to recognize design faults in a device as early as possible during the project. The advantages are obvious. Since the testing of basic inverter functions is only possible after the e-motor controllers have been implemented, then the project has already reached an advanced stage. Ideally, a test system should require a high degree of unit-under-test maturity and allow fault-tolerant testing at very early stages of the project.
Reproducibility tests are a further quality feature of a test solution
This holds true for both the test instrumentation and the unit-under-test. Test equipment that require “golden samples” or very specific special provisions quickly develop into a problem. The special provisions can be damaged and are also often irreplaceable because their replacement influences the test results rendering them non-reproducible. The topic of wear also needs to be mentioned, for example if real e-motors are considered for use as test loads for a drive inverter. The unit-under-test itself is also subject to these limitations since it often has to be adapted for a test layout. This can affect both the hardware and the software. A reliable test solution therefore does away with such special provisions and does not require any form of unit-under-test adaptation.
Controllable test conditions
The ability to influence the unit-under-test’s interfaces is a further feature of a good test solution. This not only includes parameters such as the drive inverter’s supply voltage or the provided torque, but also values such as the flow and temperature of cooling media. Even the electro-magnetic characteristics of a connected electric motor are also important in this consideration. The use of emulators offers enormous advantages since the characteristics of an emulated e-motor can be controlled via parameters.