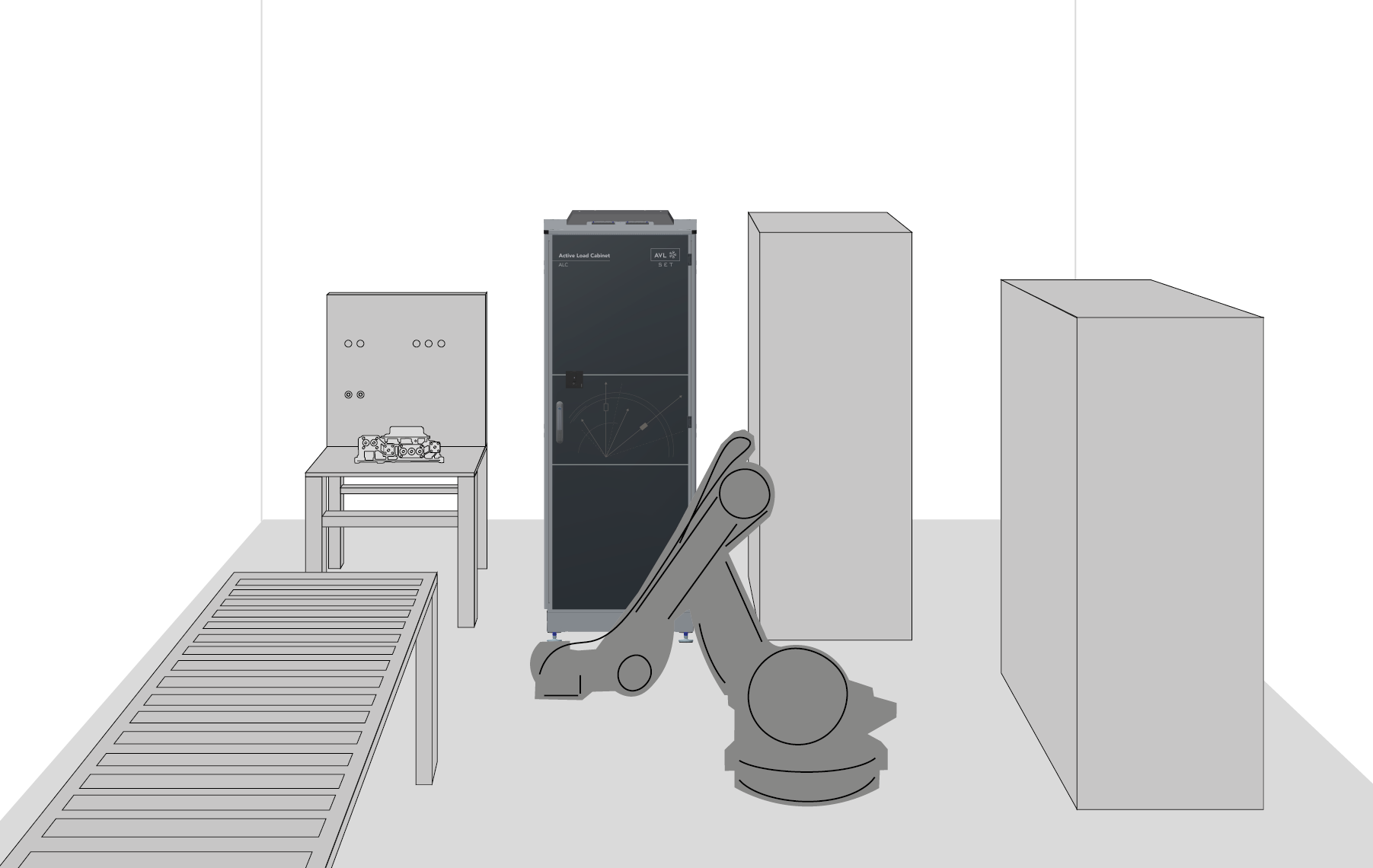
Use Case 1
Active Power Test
How to stress the inverter with active power to verify the required functionality?
As the number of electric vehicles is increasing, more and more electric components like inverters need to be produced. Before the inverter is installed in the vehicle, a customer defined test content is performed at the End-of-Line. High-voltage (HV) functional tests at the end of the assembly line are essential for the inverters’ quality and functionality check.
With these HV functional tests, the correct and desired functionality of the produced inverter can be verified. In this case, the ALC acts exclusively as an R-L load, the evaluation of the results is carried out by the higher-level control system. As a result, the inverter is classified as passed or failed. Reasons for failed may be for example assembly faults or component defects. The so-called active power tests need to be executed as fast and easy as possible.
​
The R-L mode of the AVL Active Load Cabinet is the key product of the functional test of the unit under test (UUT) at critical operating points. Due to the active power, the UUT is stressed on both, the AC and DC sides. By having the power flow closed via the DC link between the ALC and the UUT, only the losses of the ALC and the UUT need to be drawn from the grid. With the use of our ALC, power circulates in the system and is not primarily converted to heat (= losses).
This results in significantly lower operating costs of the complete testing environment due to highest energy efficiency in the Active Load Cabinet.
Furthermore, compared to a passive load, the ALC operates with both, active and reactive power. This allows to test the UUT’s power electronics under more realistic conditions. The R-L mode is used for example to detect wrong functionalities in the UUT hardware and is therefore essential for quality checks.
​
​
Use Case 2
UUT Sensor Calibration
How to choose appropriate current sensors for the inverter?
During the inverter development phase, decisions regarding subcomponent materials need to be taken. Choosing the appropriate current sensors is a major challenge due to the contradiction accuracy vs. costs. When low-cost current sensors are used, a possible bad behavior needs to be accepted, otherwise expensive current sensors need to be taken.
In general, if the sensor measures incorrectly, the inverter controls the e-motor incorrectly, which could lead to an undesired behavior.
In calibration mode, the AVL Active Load Cabinet acts as a variable current source. Here, the ALC drives a desired DC current through the UUT to determine measurement deviations by the UUT-internal current sensors.
This is done by comparing the current controlled by the ALC, which is measured by an external measurement device, with the value determined by the UUT-internal current sensors.
It should be noted that the ALC acts exclusively as a variable current source, the measurement deviations must be determined by the higher-level control system.
Thanks to the precise current from the ALC, excellent calibration results can be expected. This eliminates the need to move the inverter again which leads to an optimized cycle time.